Good Manufacturing Practice (GMP) Guide for Temperature Monitoring Compliance
Temperature monitoring is a critical aspect of Good Manufacturing Practice (GMP) in various industries, including pharmaceuticals, food processing, and storage facilities.
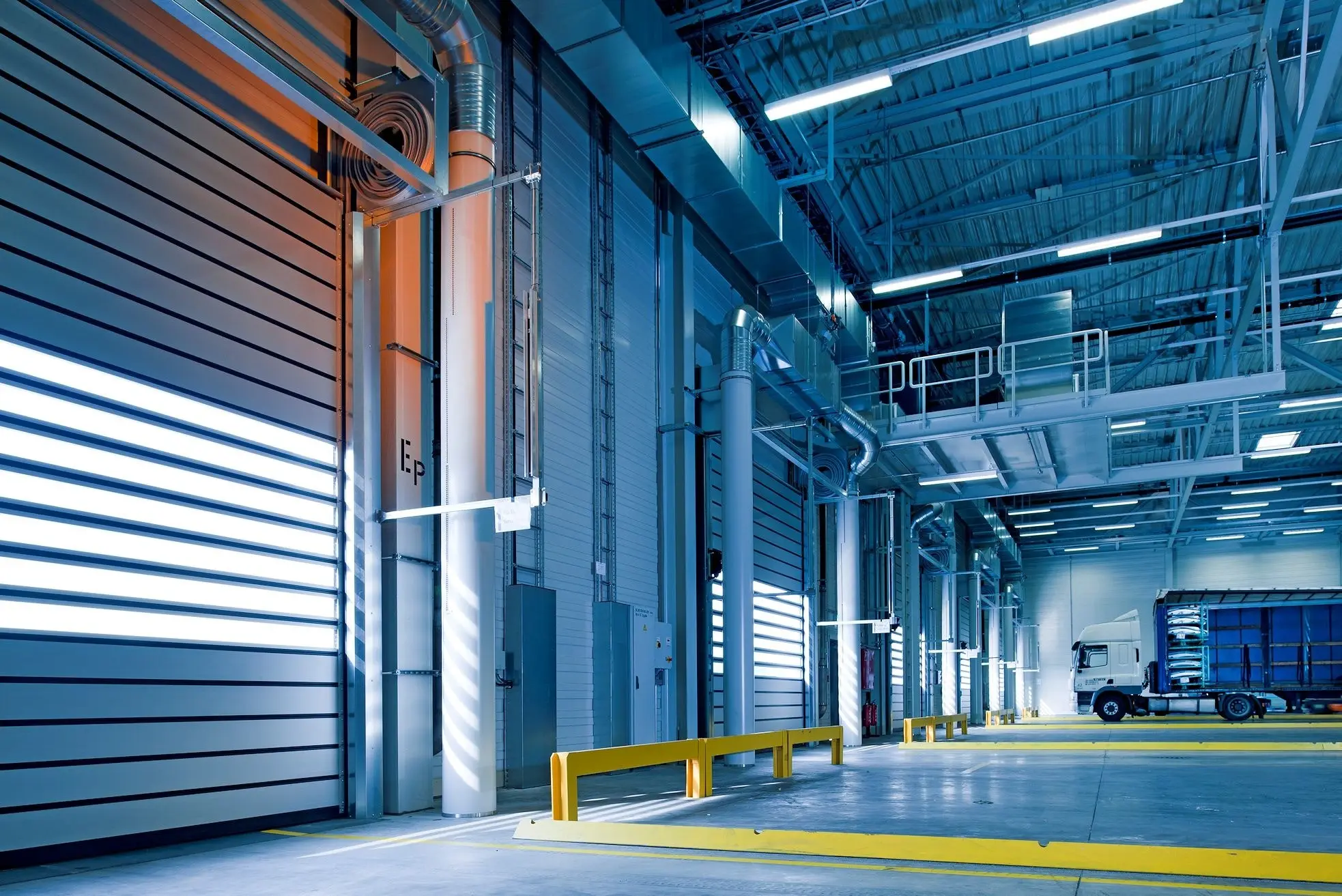
What is Temperature Monitoring?
Temperature monitoring is a critical aspect of Good Manufacturing Practice (GMP) in various industries, including pharmaceuticals, food processing, and storage facilities. Accurate temperature control and monitoring of the same is vital in maintaining product integrity and compliance with exacting global standards.
In this blog post, we delve into GMP temperature monitoring guidelines and highlight the key aspects relating to FDA requirements, temperature control, guidelines for monitoring, and more.
Temperature is a measurement of the intensity of heat present in a substance or environment. In GMP settings, temperature monitoring involves systematic collection and analysis of temperature data to ensure that critical storage areas, equipment, and processes maintain the required temperature ranges.
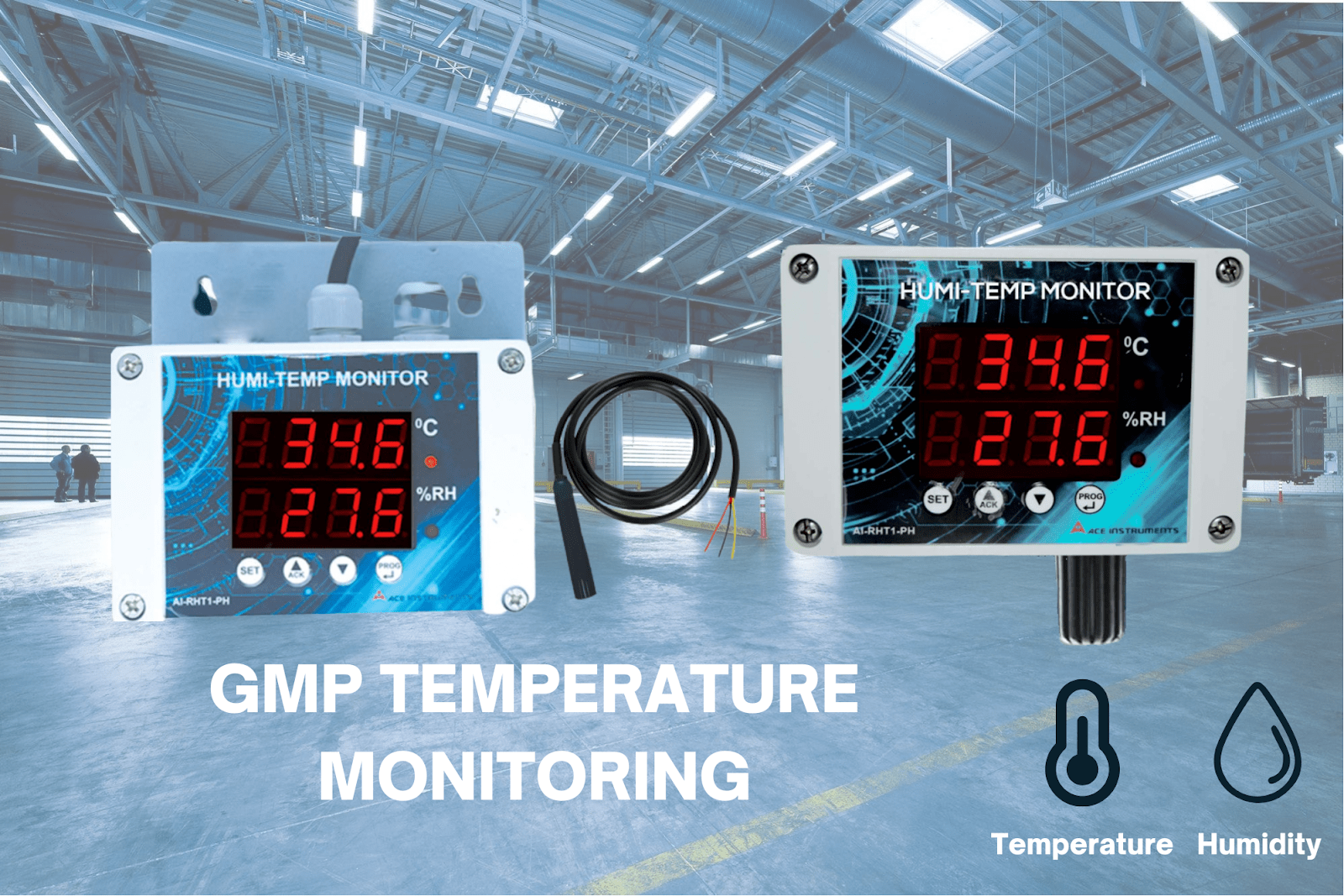
Why perform GMP Temperature Mapping?
Performing GMP temperature mapping is essential in understanding the temperature distribution within a facility or a specific storage area. The process involves placing temperature sensors throughout the space to collect data and create a detailed temperature map.
It is essential that large commercial refrigerators and walk-in cold rooms are monitored with an electronic temperature monitoring device that is able to measure load temperatures in more than one location.
When certain products are exposed to, and stored in, incorrect temperatures, their quality is no longer guaranteed. In the pharmaceutical, cosmeceutical, and food industries, temperature monitoring is even more essential as consumers’ lives are at risk in the case of improper storage.
Temperature mapping helps identify hot and cold spots, temperature gradients, and any areas where the temperature may deviate from the desired range. This information enables proper planning and implementation of corrective actions to ensure consistent temperature control and product quality.
GMP Temperature Mapping vs Calibration
Temperature mapping and calibration are two distinct processes within temperature monitoring. On one hand, calibration involves verifying and adjusting the accuracy of temperature sensors and instruments. It helps ensure that the temperature measurements provided by the devices are reliable and within acceptable limits. Calibration is typically performed using certified calibration equipment or through accredited calibration laboratories.
On the other hand, temperature mapping focuses on assessing the temperature distribution within a given space. It involves strategically placing sensors in different locations to capture temperature variations. Temperature mapping provides a comprehensive understanding of temperature conditions throughout a facility and, enables effective control and monitoring.
Choosing the Most Suitable Technology for your needs
Choosing the right technology for temperature monitoring is crucial in ensuring accurate and reliable measurements. Several options are available, with the most common being combination monitors to measure temperature and humidity, like the AI-RHT1-PH, with built-in and external sensors.
Factors like the nature of the products being monitored, the size of the facility, and the required level of data accessibility must be considered when selecting the technology.
Digital data logging devices are portable and cost-effective solutions that record temperature data at predefined intervals. Not only do they satisfy the requirements of the European standards to provide suitable temperature and relative humidity monitoring for stored pharmaceuticals and other sensitive medical equipment, but they are also suitable for small-scale monitoring applications. Temperature monitoring systems provide advanced features like automated alerts, data analysis, and centralized monitoring, making them suitable for complex and critical environments.
Best Practices for Sensor Calibration
Regular calibration of temperature sensors is essential in ensuring accurate measurements. The following are some of the best practices for sensor calibration:
- Use certified calibration equipment or accredited calibration laboratories.
- Establish a calibration schedule based on the manufacturer's recommendations, industry guidelines, and regulatory requirements.
- Perform calibration in a controlled environment with stable temperature conditions.
- Keep detailed records of calibration dates, results, and any adjustments made.
- Implement a calibration deviation protocol to address out-of-tolerance conditions promptly.
The AI-RHT1-PH comes with traceable calibration certificates (calibrated from factory) for the accurate monitoring of temperature and humidity.
How to Cost-effectively Meet Your Compliance Obligations
Meeting compliance obligations can be achieved in a cost-effective manner by following these steps:
- Understand the regulatory requirements specific to your industry, such as FDA temperature monitoring requirements.
- Conduct a risk assessment to identify critical temperature-controlled areas, products, and processes.
- Develop a robust Standard Operating Procedure (SOP) for temperature monitoring that includes guidelines for equipment, data collection, analysis, and corrective actions.
- Invest in reliable and accurate temperature monitoring technology that aligns with your specific needs.
- Train staff on proper temperature monitoring procedures and data interpretation.
- Regularly review and audit your temperature monitoring practices to ensure ongoing compliance.
GMP Temperature Monitoring in a Nutshell
GMP temperature monitoring is a vital aspect of quality control and regulatory compliance in various industries. It ensures that temperature-sensitive products and processes are maintained within specified ranges, preserving product integrity and consumer safety. By understanding the principles of temperature monitoring, including temperature mapping, calibration, technology selection, and best practices, organizations can effectively meet their compliance obligations while optimizing operational efficiency and cost-effectiveness.
Contact us today to customize your GMP temperature solutions. Our existing product range includes the following solutions suited to assist in GMP temperature monitoring: AI-RHT1-PH (built-in sensor), AI-RHT1-PH (external sensor).
FAQs about GMP Temperature Monitoring Guidelines
What is the ideal temperature for GMP?
GMP does not specify a single temperature requirement. The temperature for GMP depends on the specific industry and the products or processes involved. Each industry may have different temperature ranges based on product stability, safety, and regulatory requirements.
What is the temperature limit in Pharma?
The temperature limits in the pharmaceutical industry vary depending on the specific drugs and their storage requirements. It is essential to follow the guidelines provided by drug manufacturers and regulatory bodies, such as the FDA, to ensure product stability and efficacy.
The WHO guidelines recommend the following:
- Store frozen: transported within a cold chain and stored at -20°C (4°F).
- Store at 2°-8°C (36°-46°F): for heat-sensitive products that must not be frozen.
- Cool: Store between 8°-15°C (45°-59°F).
- Room temperature: Store at 15°-25°C (59°-77°F).
What are GMP conditions?
GMP conditions refer to the set of guidelines and regulations that ensure the quality, safety, and efficacy of pharmaceuticals and other products. These conditions cover various aspects, including facility design, equipment calibration, personnel training, documentation, and temperature control.
How is temperature monitored in SOP?
Monitoring temperature in an SOP typically involves following established procedures for data collection, analysis, and corrective actions. This may include using calibrated temperature sensors, maintaining temperature logs, conducting regular temperature checks, and implementing appropriate corrective measures when temperature deviations occur.
What are the basic requirements of GMP?
The basic requirements of GMP include ensuring facility cleanliness, proper documentation, personnel training, equipment calibration, process validation, quality control, and temperature control. These requirements aim to maintain product quality, safety, and consistency.
What is the temperature range for GMP?
The temperature range for GMP varies depending on the specific industry, products, and regulatory requirements. It is essential to determine the appropriate temperature range based on product stability, safety, and industry guidelines to ensure compliance with GMP standards.
Know the latest trends in IAQ solutions from the Ace Instruments team
Instruments that exceed your technical expectations
Comprehensive and customized IAQ solutions for all applications